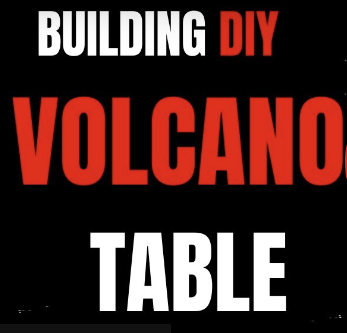
In this video I turn a slab of Silver Maple into a Live Edge Volcano Table.
Transcrip
hey it’s Jordan with studio gbk and
today I take a slab of silver maple Bust
It Down burn it and turn it into a lava
table everything went pretty well until
I got the worst leak I’ve ever had
during a por so stay tuned for that now
I bought this slab in March of 2023 for
only $50 and the fact that it’s cracked
is what made it so cheap I was actually
buying some Walnut when I noticed this
piece on the side and she was damaged
and looked like she’d been through a lot
but I saw potential and decided to give
it a chance as you can see I removed all
of the bark from this slab first and I
wasn’t sure on how I was going to break
this up and some of you might be
wondering why I wanted this breakup in
the first place well number one is
because it’s fun to break things but
jokes aside I saw this beautiful table
on Instagram that inspired this design
along with Woodworkers in Russia or some
country that I don’t speak the language
making amazing volcanic tables along
with these patio tables kitchen islands
and even rugs which aren’t real they’re
AI generated but I believe I’m capable
of making something very close to it and
I will so here’s my first attempt I
thought of using a bat or a mallet but
instead I tightened this clamp to the
side of my workt and smashed the pieces
on top of it I took the broken pieces
and rearranged them in the same order as
they were before I broke the slab to
give it that explosion effect and I put
them on top of a piece of cardboard so I
could trace this awkward shape and cut
it out and begin making mold now this is
the strangest and most difficult mold
I’ve ever built because it isn’t square
or rectangular like most molds typically
are it’s Live Edge all the way around so
I wasn’t sure how this would work out
but I put that cardboard stencil on top
of the white MDF board trace the same
shape all the way around and cut along
that line with my jigsaw I just used
some extra MDF that I had on hand and I
ended up using two different pieces to
make that full shape and I was actually
pretty pleased with how close I was able
to get it to the actual shape of the
wood I came back with my torch and
burned all these pieces individually on
the top bottom and sides this took me
like8 hours in total and I could have
used a more powerful torch to speed up
the process but I didn’t want the pieces
to warp so I used this little torch
which stopped working Midway through the
process after taking it apart and still
having trouble I bought a new one and
managed to get all the pieces to that
natural charred black color that I
wanted I sealed them with art resin to
preserve that color and protect them
from moisture and water and here’s what
they looked like when I finished I let
them dry for 72 hours and as you can see
the little drips and excess hardened at
the bottom but I just removed it with a
chisel and the rest of it I sanded after
that I was ready to build the mold so I
cocked in between those two pieces and
connected them well actually three
pieces with that little guy there I
covered the entire surface with tuck
tape so the epoxy doesn’t bond to that
white MDF board then I used this
flexible garden edging to go around the
perimeter of this mold no I did not come
up with that idea myself it was a tip
from another woodworker I put a bunch of
cocking around the entire edge of the
mold and used these drywall screws to
attach it it took a lot of them but I
was more worried about this thing
leaking than I was about wasting screws
so I went pretty crazy with the screwing
on this one I was so worried about a
leak that I came back with an extra beat
of after it was already screwed
just to make sure that this was sealed
to Perfection and if you’re thinking
about anything other than this mold
right now and the wood that’s about to
go inside of it you should probably get
some help um I cleaned off my finger and
put those pieces back inside the mold
they fit pretty well but the Live Edge
is not shaped at a perfect 90° angle so
there were areas that I had to bend the
garden edging so the pieces could sit
flat I used my torch to heat it and bend
it and I even cut it in some are areas
and then used a bunch of Tuck tape to
control where the epoxy would go and
attempted to make the perfect Edge that
I was going for and at that point I
really didn’t know if this would work or
not but I’m going for it I used clamps
and wood and red tape to hold these
pieces and stop them from moving once I
pour probably not the textbook way to do
this but feel free to comment with any
ideas that you have at this point I’m
ready to pour the table now my goal here
is to color the epoxy as close to a
volcanic lava fire color as possible and
this is my first attempt at a volcano
table so I’m hoping for the best after
looking at some pictures online I
remixed these high flow acrylics from
Golden pigment I used napthol redl and
mixed it with pyro orange and that just
sounds like Fire doesn’t it so I mixed
them all together with epoxy and to be
honest this turned out to be a bit more
red than I wanted and I would would have
added more orange but I had already
mixed in too much dye which can affect
the consistency and how well the epoxy
dries so I just poured it as is and
hoped for the best I also put some of
that same epoxy in this ketchup looking
bottle that you see here and use that to
fill in these cracks and voids in the
surface of the table I could have just
used clear but I want the little cracks
and veins in the wood to match these
lava rivers that the table is made up of
and I wasn’t too worried about getting
it neat because I’ll sand it later
anyway I just want to make sure the
voids are all the way full and as I did
this on the surface it started looking a
bit more orange and lava like so I was
actually pleased with how that color
combination turned out I also added some
yellow pigment into the mix and spread
it around with a piece of this Popsicle
stick and at this point I kind of wish
that I’d given myself more space to work
with because trying to swirl these lava
designs into the epoxy with hardly any
space was very challenging and even
irritating later on when tons of it
dried on my live edges and I had to come
back and scrape it all off which took
hours and I wanted to just let it go but
the perfectionist in me just wouldn’t
allow it so I scraped and sanded and
even recolored these black edges with a
marker after that I mixed and poured the
clear layer and as you can see this had
way too many bubbles but I was able to
use my torch and heat gun to eliminate
them and I could have used that lava
color all the way through but my goal
was to keep as much of the Live Edge
visible as possible which is why I
poured the clear over the top of that
Lava River and during this clear pour
was when it started to leak oh my
gosh
why and this is my first time dealing
with a leak so I wasn’t sure what to do
here I’ve heard Flex Seal works but I
didn’t have any on hand and I didn’t
have time to go grab it so I just
started covering that area with red tape
as fast as I could and after using a
bunch of tape it still kept on
leaking oh this is
bad oh this is
bad so I added more tape and more tape
and layered tape on top of tape until I
couldn’t add any more and after all that
it still dripped a little but my tape
job did minimize the leak and I covered
it to prevent dust or bugs from ruining
the clear layer and left it to dry when
I came back it actually dried fairly
well and clear and I was glad all my
resin didn’t leak out onto the floor but
it did have these clusters of bubbles
that dried onto the surface and you know
bubbles are cool and all when you’re a
kid but in the epoxy game they’re the
last thing you want to see in your
finish they’re also permanent just like
face tats so I actually cut out this
area that was really bad and filled it
with black epoxy to make it look like it
was a part of the wood rather than me
being an amateur at pouring clear epoxy
and if you can’t tell by now I was
really starting to regret this clear
layer idea and to top it off when I
poured the final layer of clear it had
even more bubbles than the previous
layer and ruined any chances that I have
of this looking like clear glass and at
this point I just want to throw the
whole thing away but I kept going and
removed all the screws peeled off the
garden edging and took this out of the
mold removing it from the mold was
pretty
easy but I did have to cut off a bunch
of excess clear epoxy that dried around
the edges luckily it was pretty soft
because it hadn’t fully cured and after
cleaning up those edges I threw it in
the back of my truck along with some
other projects and took it to Ponderosa
Mill Works in Oakland to send it through
the the wide belt
sander
all right these machines can cost
well over
$100,000 so being able to use this for
$200 an hour is actually a really good
deal so when people ask me hey bro can I
have a table for
$200 I say yeah you can go to IKEA they
sell tables for 200 bucks maybe less um
anyways after sending it through the
planer a couple times it completely
removed the black charred layer that I
had worked so hard to burn and I did not
see this one coming and this was just
another issue out of many with this
table so I took it back to my shop and
cut off more of that clear epoxy that
had dried around the edges and I sanded
both sides down as smooth as possible to
remove those lines but at this point I
was just done with this table and I felt
like cutting it up and throwing it away
but instead of doing that I let it sit
in my shop for months started some new
projects and just recently decided that
I do my best to finish it even though
it’s not exactly what I want so I
flipped it over and decided to use the
bottom side as the surface even though
this wasn’t the original plan and this
led to me cutting off even more of that
clear epoxy from the edges and I just
wondered is this still considered a
natural Live Edge or is it considered a
GMO unnatural Edge now that I’ve
interfered with it let me know in the
comments I sanded the whole thing down
some of it by hand the rest with my
orbital sander and after sanding it all
the way up to 400 grit I used this true
black wood stain from Home Depot to
stain the wood black and bring it back
to that original color that I wanted
when I first started started burning it
now this is obviously artificial but I’m
happy with how close this color is to
the original color that I had wanted I
stained the bottom first to get some
practice strokes in and the bottom won’t
really be seen much but you never know
when someone might have their face down
there cleaning or whatever and if they
do I would want them to be
impressed I flipped it over and stained
the top of this table which used to be
the bottom and this really brought out
my artistic side more than any other
project that I’ve done I used a tiny
paintbrush to make sure I stayed inside
the lines and I remember being forced to
color things back in elementary school
which I always thought was stupid but
little did I know this was a valuable
skill that would be very useful later in
life after staining the whole thing this
is how it looked which is not bad for a
piece that I almost gave up on um the
stain dried a little rougher than I
wanted and I didn’t want to sand it off
and ruin that black finish again again
so I just went over it with this 3000
grit sanding pad to make it smooth again
and this actually worked out pretty well
after that I was ready to attach the
legs I used these 28 in hair pin legs
and I could have done something much
fancier but at this point I just want to
be done I spread these legs out exactly
where I want them to be and used framing
squares to make them somewhat
symmetrical this is to help with balance
I marked the location of the holes with
a sharp ice pick because marker or
pencil would be hard to see on this
black finish and then I drilled the
holes for my threaded inserts a threaded
insert basically allows the legs to be
removed and reattached hundreds or
thousands of times versus screwing
straight into wood you can only remove
them a small amount of times now when I
went to screw them in they busted
prematurely before they were even all
the way in which is never a good thing
the big mistake here is that I used
brass threaded inserts when I should
have used steel silver maple is a hard
wood plus this has tons of epoxy in it
so these soft brass threaded inserts
just couldn’t take the pressure I
drilled bigger holes and was able to get
some of them in but others broke off and
I had to remove them with vice grips
some were in deep enough that I just
sanded them down and after messing with
this table for a whole year here I am
cursing at it and calling it names which
is really not how I wanted this to end
but after fighting with these inserts I
managed to get them all in and attach
the leg successfully and if you’re
wondering this is how it
felt after that I finished this off
using mineral oil and a rag I thought of
doing a clear coat but I refused to give
this table any more of my time and after
all the struggle I’m really happy with
how this one turned out and how much it
resembles lava in certain places a
volcano was the goal but my girl said
it’s a Darth Vader table and using AI
here’s how it would look in your house
or maybe even a private beach let me
know what you think in the comments and
subscribe if you enjoyed this video
thanks for watching see you on the next
one